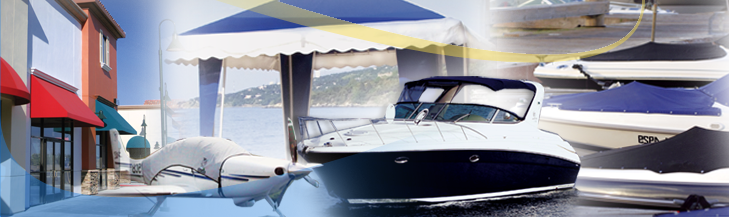
Water Repellents Pt. II
The logic behind the choice of a water repellent and the science of how they work.
Welcome to the Fall 2019 edition of Textile U. This is a follow-up to the February 2017 Textile U lesson “Post-Treatment Water Repellent”.
No matter the construction of your material, it will likely have a water repellant applied during manufacturing. Typically, certain types of water repellants are used for each specific fabric construction.
But first, let’s clear up some terms that are commonly used:
- Water Repellency: Ability of the fabric to resist being wetted by water. Water drops will roll off the fabric. Water repellent fabrics will permit the passage of liquid water once the hydrostatic pressure is high enough.
- Stain Repellency: Ability of the fabric to withstand penetration of liquid soils under static conditions involving only the weight of the drop and capillary forces.
- Water Resistance: Ability of the fabric to resist water penetrating the fabric. This is not the same as Water Repellency, even though people mistakenly use the terms interchangeably. They are related however, as if a fabric has a low Water Repellency, it will leak faster as the fabric wets out sooner allowing the water to penetrate easier.
There are three main types of water repellants that are used: Flourocarbons, Waxes, and Silicone. Let’s look at each of them in a little more detail:
Fluorocarbon
- Provides good initial spray rating (Spray Rating indicates the wettability of the solid by the liquid).
- Harder to break down by UV exposure.
- Provides good soil and stain resistance for both water & oil based stains.
- Works well at low levels, so a lower add-on allows the water vapor to pass through the fabric easier (i.e. more breathability).
- Most expensive of the three main types
- Their low surface energy allows fluorocarbons to repel oil - especially with the proper amount of the fluorocarbon on the fibers and the orientation of the closely packed fluorocarbon tails. Heat is needed to maximize the orientation.
- Fluorine-based
- EPA dictated a change from C8 to C6 a few years ago.
- Short chain PFOS (perfluorooctane sulfonate) and perfluoroocatanoic acid (PFOA) used in the production of fluorocarbons are persistent in the environment due to the strength of carbon-fluorine bonds.
- C8 has a trace possibility to generate a bi product of PFOA since C8 is a large chain molecule.
- C6 is an EPA-approved option due to its short chain and thus has a much lower tendency to create PFOA. Also, today’s fluorocarbon manufacturers have a technique that removes or decomposes any PFOA.
- For more info, click on the link from the EPA’s website: https://www.epa.gov/pfas/basic-information-pfas
Wax
- Provides good initial spray rating (Spray Rating indicates the wettability of the solid by the liquid).
- Not durable as it can be abraded by mechanical action and dissolves in dry cleaning fluids and laundry products.
- Provides good soil and stain resistance for water based stains, but not soil resistant to oil base products.
- Least expensive of the three main types.
- Typically uses paraffin and synthetic waxes
- Can yellow with age.
- Nano technology created fluoro-free hydrophobic finishes.
- Waxes with film formers can enhances the following characteristics: water repellency, anti-blocking, abrasion resistance, matting, slip, and soft feel.
- Can be combined with either Flourocarbons or Silicone.
Silicone
- Provides good initial spray rating (Spray Rating indicates the wettability of the solid by the liquid).
- Less durable than fluorochemical finishes, so UV exposure will break down water repellency sooner.
- Provides good soil and stain resistance for water based stains, but not soil resistant to oil base products.
- Work well at low levels, so a lower add-on allows the water vapor to pass through the fabric easier (i.e. more breathability).
- Less expensive than fluorochemicals but more expensive than waxes.
- Colorless, odorless, soft hand, sometimes used as a fabric softener
- Resinous polysiloxanes are durable, more resistant to abrasion and less soluble in dry-cleaning fluids or laundry products.
- Good for slip and abrasion
- Can be oily
Now let’s look at the main types of fabrics and what is typically used:
Solution-dyed Fabric (polyester and acrylic)
- Fluorocarbon treated
- Water resistant not waterproof, especially since it breathes.
- Spray Rating 100
Acrylic-coated Fabric
- Uses waxes, silicones, or fluorocarbon (typically as a film former).
- Water resistant is not waterproof, but most often is “waterproof enough” and it is more water resistant than the solution-dyed’s but breathes minimally. (Normally, the less breathable a product is the more waterproof it will be.)
- Spray Rating from 70-95
Urethane-coated Fabric
- Uses waxes, silicones, or fluorocarbon (typically as a film former).
- Aromatics urethanes yellow upon weathering.
- Spray Rating from 70-95
Vinyl-coated Fabric
- Uses waxes, silicones, or fluorocarbon (typically as a film former).
- Are non-porous and are almost waterproof, at least until the vinyl degrades.
- Limited to no breathability
- Stiffens upon outdoor exposure and cold temperature.
- Spray Rating from 70-95
Knowing and understanding types of water repellents and the types of fabrics upon which they’re used gives you greater knowledge of the issues of water repellency, and allows for you to make better decisions when asked to provide solutions to issues involving water and keeping it away with the use of fabric.