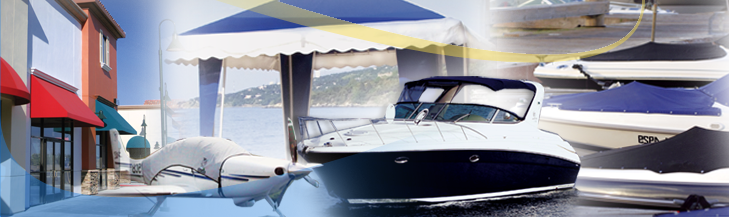
Polyester 101
Welcome back to School! This is a Marlen Textile U course covering:
Polyester 101
Question: What is both a movie and a fabric?
Answer: Polyester!
The 1981 film by John Waters is already 35 years old, but the origins of the man-made polymers and material date to 1941, when alcohols were successfully mixed with carboxyl acids to create fibers.
Marlen Textiles has some of the best-known polyester-based outdoor fabrics on the market. As such, we thought you might want to know a little more about polyester, and why it’s an important choice for fabric, especially given advances in the past 30 years.
WHAT: Polyester yarn is a man-made fiber, with the fiber-forming substance being any long chain synthetic polymer composed of at least 85% by weight of an ester of dihydric alcohol and terephthalic acid. Fabrics woven or knitted from polyester thread or yarn are used extensively in apparel and home furnishings, from shirts and pants to jackets and hats, bed sheets, blankets, upholstered furniture and computer mouse mats. Industrial polyester fibers, yarns and ropes are used in tire reinforcements, fabrics for conveyor belts, safety belts, coated fabrics and plastic reinforcements with high-energy absorption. Polyester fiber is used as cushioning and insulating material in pillows, comforters and upholstery padding. Polyester fabrics are highly stain-resistant—in fact, the only class of dyes which can be used to alter the color of polyester fabric are what are known as disperse dyes. Besides fabrics, polyesters are used to make bottles, films, canoes, liquid crystal displays, holograms, filters, dielectric film for capacitors, film insulation for wire and insulating tapes. They’re also widely used as a finish on high-quality wood products such as guitars, pianos and vehicle/yacht interiors.
HOW MADE: The polyester polymer is produced by the reaction of ethylene glycol and terephthalic acid or its derivatives. While highly technical, a manufacturing overview is provided here:
The first step in producing synthetic yarn such as polyester begins with the raw material known as POY (partially-oriented yarn). POY is made from small polymer beads, or chips, that are melted and extruded through microscopic holes to form a single fiber filament. The machine that does this is called a spinneret.
The single fiber filament is then typically drawn, heated and twisted to optimize various physical characteristics like bulk, strength, stretch and coating adhesion. Then some yarns are texturized to impart attributes in the woven goods that provide products with unique and superior performance characteristics. There are a variety of ways to texturize polyester yarn. A popular way is air jet, where a jet of air is shot across the yarn during production to “disrupt” the yarn and provide more surface area. The original polyester yarns were spun yarns (a yarn consisting of small pieces of fiber “stapled” back together to provide one long strand). The main use of polyester at the time was as a replacement for cotton (less expensive, not prone to mildew, etc). Then, in the early 1970’s filament yarns were able to be texturized (described above) in an effective way. Because of this, polyester was able to be spun as a filament and texturized efficiently to provide people a stronger yarn that had the attributes spun yarns provided, such as more surface area, that imparted a more “canvas” feel to the woven product.
HOW MEASURED: Polyester yarn size is measured in denier. Denier is a weight per unit length measure. It is the number of weights of 0.05 grams per 450 meter length (or weight in grams per 9000 meters of length). So a 600-denier yarn weighs 30 grams per 450 meter of length, or 0.0667 grams per meter of length). The higher the denier, the heavier and thicker the yarn is. Another popular yarn used in our industry is acrylic. Because acrylic is a spun yarn, it is not measured in denier.
WHY: As opposed to other types of yarns (i.e. cotton & acrylic), polyester yarns will not pill. Pilling is a surface defect of textiles, and is considered unsightly. It happens when normal wear and tear of the fabric causes loose fibers to begin to push out from the surface of the cloth, and, over time, abrasion causes the fibers to develop into small spherical bundles, anchored to the surface of the fabric by protruding fibers that haven't broken.
A lot of the polyester yarns used are twisted yarns, also known as ply. A 2-ply yarn is 2 strands twisted together, a 4-ply yarn is 4 strands twisted together, and so on.
WHEN: In the early 1990’s, the next advancement was the ability to make micro fiber yarns. Now, yarns could be strung with many smaller fibers, providing a yet even stronger end fabric. As a result, multi ply yarns were available in smaller and smaller total sizes.
The next advancement is currently being undertaken, and that is recycling. Most major yarn manufacturers have introduced polyester yarn made from recycled plastic, turning things such as bottles into yarn used in woven polyester goods. Right now, there is roughly a 25% premium price for the product to be made from recycled yarn. Most of the market place is not willing to pay that high of a price to be “green”, but the trend is causing the price to be driven lower and at some point it will be cost effective.
Polyester fibers have:
- High strength
- Most other yarns are much weaker and lead to tearing
- Resistance to shrinking
- Most other yarns shrink more
- Resistance to stretching
- Most other yarns stretch more leading to low spots and a place for water to collect and eventually leak
- Some other yarns actually grow when they are wet, leading to low spots and a place for water to collect and eventually leak
- Quick drying with resistance to wrinkling, crease retention and mildew formation
- Easier to maintain
- Resistance to abrasion
- Most other yarns abrade much easier and faster, leading to holes in the fabric
- Resistance to UV
- Additives can be added during the yarn production to provide increased longevity
- Melts and burns when exposed to a flame
- You can add flame retardant chemicals to the yarn when making it to provide an FR yarn, but doing so significantly lowers the strength of the fiber.